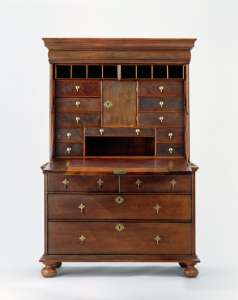
Furnituremaking
From the founding of Philadelphia in 1682 until the late 1800s, a vibrant community of cabinetmakers plied their skills alongside specialists in carving, chair making, and turning. Others who worked with wood included carpenters, coopers, shipwrights, and wheelwrights. These tradesmen were as diverse as the city itself, and their complex webs of language, ethnicity, religious ...